
42CrMo齒輪感應(yīng)器的設(shè)計與制造方法
目錄:技術(shù)支持點(diǎn)擊率:發(fā)布時間:2019-07-27 13:33:05
應(yīng)加熱淬火是熱處理的重要工藝之一,具有加熱速度快、可局部加熱、節(jié)能、清潔、易于實(shí)現(xiàn)機(jī)械化及自動化等特點(diǎn),同時可提升產(chǎn)品耐磨性和硬度等性能。在齒輪的感應(yīng)加熱應(yīng)用中,按照其加熱方式,主要可以分為逐齒淬火和整體淬火。逐齒淬火由于感應(yīng)器尺寸的限制等原因,主要應(yīng)用在齒輪模數(shù)大于7的齒輪上。這種淬火方法按照加熱部位又分為逐齒齒牙淬火法和逐齒齒溝淬火法。
逐齒齒牙加熱是使用感應(yīng)器將整個齒面包絡(luò),然后進(jìn)行感應(yīng)加熱。這種方法的特點(diǎn)是齒頂和齒面加熱較強(qiáng),但是對齒根部位的加熱較弱。
逐齒齒溝加熱使用感應(yīng)器在兩齒齒溝部位進(jìn)行加熱,使用這種加熱方法能對齒根也有較強(qiáng)的加熱效果,可以獲得沿齒溝仿形的硬化區(qū)域。隨著現(xiàn)代工業(yè)對齒輪設(shè)計提出更高的要求,在中大模數(shù)齒輪中,逐齒齒溝加熱淬火的應(yīng)用也越來越廣泛。
逐齒淬火,按照淬火方式分類,還可分為埋液淬火和噴淋淬火。埋液淬火的工件與感應(yīng)器均浸沒在淬火冷卻介質(zhì)中,工件在淬火冷卻介質(zhì)液面以下進(jìn)行加熱,隨后被周圍的淬火冷卻介質(zhì)迅速冷卻。淬火冷卻介質(zhì)通常為油、水、水基聚合物等。噴淋淬火一般使用單獨(dú)的感應(yīng)器和噴淋器,使用感應(yīng)器對工件加熱,噴淋器對工件淬火冷卻。出于安全方面的考慮,淬火冷卻介質(zhì)多為水或水基聚合物。
齒輪的整體感應(yīng)加熱淬火即為一發(fā)法淬火。由于整體加熱一次性需要加熱的面積相對逐齒加熱來說要大得多,因此其加熱所需的電源供應(yīng)也就大得多。這使得其主要應(yīng)用在中小直徑齒輪中。普通的整體加熱,采用低頻電源加熱,然后噴淋或整體在淬火冷卻介質(zhì)中淬火。采用這種方法淬火,齒頂淬透和齒根淬不上火一直是其存在的主要問題。
1. 感應(yīng)器設(shè)計與制造
2009年,我公司從德國進(jìn)口一臺齒輪中頻感應(yīng)淬火機(jī)床,采用IGBT逆變電源,頻率為4~10kHz,采用水基聚合物水溶液作為淬火冷卻介質(zhì)。共有三路淬火液噴淋,一路主噴淋,兩路保護(hù)噴淋,以防止已淬火齒被回火。結(jié)構(gòu)上采用懸臂式主架,伺服電動機(jī)直接分度轉(zhuǎn)臺。由于是新機(jī)床新的感應(yīng)器結(jié)構(gòu),在感應(yīng)器制作方面與我公司之前的埋液淬火感應(yīng)器制作存在很大不同(見圖1),在消化吸收進(jìn)口感應(yīng)器圖樣的基礎(chǔ)上,結(jié)合我公司現(xiàn)有設(shè)備及技術(shù)能力,總結(jié)出了新的感應(yīng)器設(shè)計結(jié)構(gòu)及制作方法。
圖1 感應(yīng)器外形結(jié)構(gòu)
感應(yīng)器設(shè)計流程為:齒輪齒形模擬→確定間隙參數(shù)→感應(yīng)器齒形平面設(shè)計→三維建模(管路設(shè)計)→出二維工程圖。
感應(yīng)器的制作流程為:毛坯鍛造→毛坯線切割→鉆孔→成品線切割→焊接→修形→裝配→測試。
新的感應(yīng)器設(shè)計結(jié)構(gòu)及制作方法主要有以下特點(diǎn):
計算機(jī)輔助設(shè)計感應(yīng)器
新的感應(yīng)器設(shè)計更多地采用了計算機(jī)輔助設(shè)計。在齒輪的設(shè)計階段,就可以使用CAD等軟件結(jié)合齒輪滾刀、銑刀參數(shù)精確模擬出實(shí)物齒形。這樣在齒輪的設(shè)計階段就可以同時進(jìn)行感應(yīng)器的設(shè)計,而不用像以往那樣等到實(shí)物齒輪滾齒后根據(jù)實(shí)際齒形才能進(jìn)行感應(yīng)器設(shè)計、制作,節(jié)省了大量時間。
在設(shè)計方法上,使用Pro-E軟件三維立體建模設(shè)計。使用立體建模,可以更加方便地考慮感應(yīng)器設(shè)計時整體結(jié)構(gòu)、內(nèi)部管道分布、固定方式。
感應(yīng)器內(nèi)部結(jié)構(gòu)設(shè)計
新的感應(yīng)器在結(jié)構(gòu)上有了很大改進(jìn)。采用了水路、電路只有一個進(jìn)口的快接接頭。此外,還重新設(shè)計了感應(yīng)器頭部與導(dǎo)線之間的接頭方式,使用了燕尾楔結(jié)構(gòu),這樣的結(jié)構(gòu)在焊接時更方便定位找準(zhǔn),提高加工精度。
機(jī)械加工方法 在機(jī)械加工方法上將以前的大部分銑削加工,改為了線切割加工。線切割加工可以很好地對齒部仿形部位進(jìn)行加工獲得足夠的精度。
通過合理的安排機(jī)械加工步驟,簡化了感應(yīng)器的制作流程。
焊接方法
采用銀釬焊作為新型感應(yīng)器的焊接方法。銀焊絲的熔點(diǎn)較低,可以在相對較低溫度下進(jìn)行焊接,且銀釬料的流動性、在純銅表面的潤濕性也很好,因此制作出的感應(yīng)器精度高、外表美觀。
2. 試驗
在感應(yīng)器設(shè)計中,感應(yīng)器同樣還有其他的細(xì)節(jié)對感應(yīng)淬火的效果產(chǎn)生至關(guān)重要的影響。一是感應(yīng)器導(dǎo)磁體區(qū)域高度占整個感應(yīng)器高度的比值,另一個是感應(yīng)器導(dǎo)磁體材料的選擇。
因此,在以上設(shè)計點(diǎn)的基礎(chǔ)上,針對以上兩點(diǎn),主要進(jìn)行了以下兩個工藝試驗。
(1)試驗一
?。簩?dǎo)磁體高度對淬火效果的影響 試驗齒輪為某型號機(jī)車從動齒輪,齒輪材質(zhì)為42CrMo,齒數(shù)82,模數(shù)10。導(dǎo)磁體材質(zhì)均為0.2mm厚度的冷軋取向硅鋼片。試驗設(shè)備為EFD齒輪中頻感應(yīng)淬火機(jī)床。試驗變量為導(dǎo)磁體區(qū)域高度。感應(yīng)器頭部結(jié)構(gòu)如圖2所示。1#感應(yīng)器的上導(dǎo)線、導(dǎo)磁體空間、下導(dǎo)線距離比例為10.5:9:10.5。2#感應(yīng)器的上導(dǎo)線、導(dǎo)磁體空間、下導(dǎo)線距離比例為9.5:11:9.5。兩個感應(yīng)器上下端面總高度均為30mm。由此可見,1#感應(yīng)器中導(dǎo)磁體空間比2#感應(yīng)器中導(dǎo)磁體空間低了2mm,導(dǎo)磁體空間占總高度的比值,1#為3/10,2#為11/30。
圖2 感應(yīng)器頭部各部位示意
在工藝試驗中,電流為60A,電壓為230V,功率65kW,頻率9kHz,走行速度6mm/s。試驗結(jié)果如表1所示。
從表1可見,1#感應(yīng)器淬火處的齒根硬化層較2#感應(yīng)器淺,節(jié)圓硬化層較2#感應(yīng)器深。
(2)試驗二
:導(dǎo)磁體材質(zhì)對淬火效果的影響 試驗齒輪為某型號機(jī)車從動齒輪,齒輪材質(zhì)為42CrMo,齒數(shù)82,模數(shù)10。采用同樣的新設(shè)計方法、新制作工藝的感應(yīng)器。試驗設(shè)備為EFD齒輪中頻感應(yīng)淬火機(jī)床。
試驗變量為導(dǎo)磁體材質(zhì)。3#感應(yīng)器導(dǎo)磁體材質(zhì)為Fluxtrol A(鐵氧體軟磁材料);4#感應(yīng)器導(dǎo)磁體為冷軋取向硅鋼片(日本)。二者主要性能對比如表2所示。
電流為60A,電壓為230V,功率36kW,頻率9kHz,走行速度6mm/s。試驗結(jié)果如表3所示。
從表3可見,3#感應(yīng)器淬火處的齒根、節(jié)圓硬化層均較4#感應(yīng)器淺。
同時試驗中發(fā)現(xiàn),在4#感應(yīng)器中,由于取向硅鋼片中的“鐵損”,導(dǎo)致感應(yīng)器工作時硅鋼片不能很好地散熱,當(dāng)功率增加至75kW時,硅鋼片的溫度已經(jīng)達(dá)到670℃,已經(jīng)超過其居里點(diǎn)。
而鐵氧體軟磁材料雖然其居里點(diǎn)較低,但是在實(shí)際應(yīng)用中發(fā)現(xiàn),當(dāng)加載功率至110kW時,其產(chǎn)生的熱量仍不多,測量其表面溫度在100℃以下。但由于其力學(xué)性能差,局部區(qū)域經(jīng)過多次熱沖擊以后無法保持原形狀而破裂,無法繼續(xù)使用。因此,在低功率情況下,還是使用硅鋼片為宜。
3. 試驗結(jié)果分析
在試驗一中,感應(yīng)器的導(dǎo)磁體空間高度對齒輪感應(yīng)淬火后的效果有很大影響。在其他條件同樣的情況下,1#感應(yīng)器與2#感應(yīng)器淬火出來的效果有很大差別,尤其是對于齒根部位的影響。在齒輪感應(yīng)器中,感應(yīng)器的上導(dǎo)線負(fù)責(zé)對齒溝兩側(cè)齒面的預(yù)熱,感應(yīng)器的下導(dǎo)線負(fù)責(zé)對齒溝兩側(cè)齒面的加熱,加熱至淬火溫度。感應(yīng)器中間的鼻尖區(qū)域負(fù)責(zé)對齒根的加熱。
試驗一中1#感應(yīng)器的導(dǎo)磁體空間高度相對2#感應(yīng)器降低了2mm。因此“鼻尖”處的感應(yīng)器有效加熱區(qū)也就變短了,對齒輪齒根的加熱作用也就更弱了。由于加熱作用的減少,使得齒輪齒根部位的硬化層降低。同樣,由于上下導(dǎo)線占整個感應(yīng)器高度的比重升高,使得感應(yīng)器對齒輪兩側(cè)齒輪的加熱作用增強(qiáng),導(dǎo)致齒輪兩側(cè)的硬化層也增強(qiáng)了。
在試驗二中,二者材料飽和磁通密度接近,鐵氧體軟磁材料的初始磁導(dǎo)率和最大磁導(dǎo)率均遠(yuǎn)小于硅鋼片。導(dǎo)磁率越小,說明材料的聚磁能力越小。反應(yīng)到試驗結(jié)果上,可得知由于導(dǎo)磁體對磁力線的聚集作用較小,因此,其加熱后淬火的硬化層深也相對較淺。
在隨后的試驗過程中,使用鐵氧體導(dǎo)磁材料的3#感應(yīng)器能在110kW功率下應(yīng)用??赡苁怯捎谑褂玫氖钦w導(dǎo)磁體,同時上下導(dǎo)線對整個導(dǎo)磁體的冷卻作用才使得導(dǎo)磁體的溫度低于10℃。而在使用硅鋼片的感應(yīng)器中,由于硅鋼片本身在感應(yīng)加熱過程中發(fā)熱(鐵損)。硅鋼片之間的絕緣云母片同時又能絕熱,使得產(chǎn)生的熱量不能及時散發(fā),冷卻導(dǎo)磁體。因此,熱量的逐漸積蓄,使得在75kW的情況下,硅鋼片已經(jīng)嚴(yán)重超溫??梢娪捎阼F損,硅鋼片僅能用于低功率條件下齒輪的感應(yīng)加熱淬火(≤50kW)。
4. 結(jié)語
(1)在設(shè)計中,全部采用了計算機(jī)模擬設(shè)計。在管道設(shè)計中,采用了三維建模,在設(shè)計過程中就能減少感應(yīng)器可能出現(xiàn)的設(shè)計問題。
(2)在制作中,規(guī)范感應(yīng)器的加工步驟最大限度地減少了人為因素,保證了感應(yīng)器的機(jī)械精度。采用了精確配對的燕尾楔形槽設(shè)計,保證了焊接定位的精度,也就從這兩個方面上保證了感應(yīng)器的加工質(zhì)量。
(3)通過對比試驗,優(yōu)化了感應(yīng)器的上下導(dǎo)線的距離,使感應(yīng)器滿足齒輪節(jié)圓和齒根的有效硬化層要求。
(4)通過對比試驗,研究了不同導(dǎo)磁材料對感應(yīng)淬火的影響,在低功率的感應(yīng)淬火條件下,導(dǎo)磁材料優(yōu)選硅鋼片。
網(wǎng)站首頁 | 公司簡介 | 資質(zhì)榮譽(yù) | 高速鋼 | 熱作工具鋼 | 產(chǎn)品中心 | 新聞中心 | 技術(shù)支持 | 常見問題 | 聯(lián)系我們 |
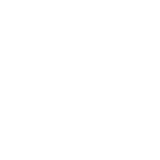
東莞市奧泰特殊鋼材有限公司 版權(quán)所有© Copyright 2017
電 話:0769-88704912
18688669368(微信同號)
傳 真:0769-88705839
公司地址:東莞市高埗鎮(zhèn)冼沙三坊高龍路段128號 備案號:粵ICP備19054886號-1
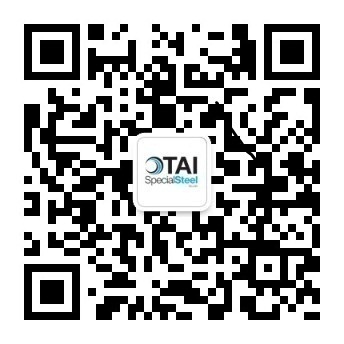